Technical Articles
Methods Used to Make Body of Ball Valves
Posted: 2015-02-26 01:17:40 Hits: 1536
Ball valves are a kind of valves rotating core to open or close valves. Ball valves have small volume and can be processed into large dimension. Ball valves have reliable sealing, simple structure, convenience for maintenance. Sealing face is closed with sphere. For this, sealing face is not easily washed by media. Ball valves have been widely used in various industries. Both ball valves and plug valves belong to the same type of valves. There are three methods used to make body of ball valves: casting, forging and spinning.
Casting
Casting is a conventional processing method. Casting requires a set of thorough smelting, pouring and other equipments. It needs large factory, many workers, large investments, many processes and complicated manufacturing technique. Casting may also cause pollution to environment. Workers’ technological level in every process has direct influence on quality of products. Leakage of pore on ball has not yet been solved. Workblanks processing has many allowances and large wastage. In general, casting flaws may result in scrap, increasing the cost of products. Quality cannot be ensured.
Forging
Forging is another processing method adopted by valve manufacturers in China. There are two kinds of processing. One is to cut off round steel. Then forge the materials into sphere solid workblank by heating. Machining is the last. The other is to press the stainless steel plate whose cutting stock is round into hollow hemispherical workblanks. Butt-weld workblanks into ball workblanks for further machining. This method has higher utilization of materials. However, it needs high-power press machine, heating furnace and argon lone welding equipments. It needs about 3 million RMB investments so that productivity can be formed.
Spinning
Spinning is a kind of advanced processing method with less or no smear metal, which combining the technological characteristics of forging, squeezing, pressing and rolling. It has high utilization of materials, saving large amount of processing time. The strength of materials can be increased by one time after being span. During spinning, spinning rollers contact with workblanks for small footprints, easy for deformation. Nevertheless, unit contact stress can be acquired with less power. So, the equipments have small volume and low total power. Spinning has already been generally accepted as a kind of energy-saving ball processing in international valve industry. It is also suitable for processing components of other hollow solid of revolution.
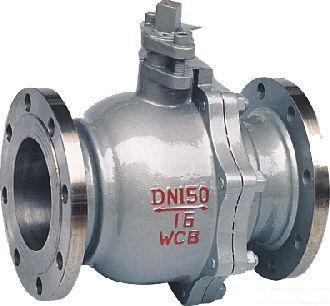